Retask air pump as crankcase vent?
#1
Inventor
Rennlist Member
Rennlist Member
Thread Starter

I had some oil squirt out of the various leak points on my cam tower seals while on the dyno the other day (at over 140MPH). I assume from crankcase overpressure.
As tested, my PCV system was free venting via a K&N breather on the oil filler cap.
My (somewhat unoriginal) new idea is to re-install the air pump, connect the intake port of the air pump to the oil filler cap via a 'T' fitting, the branch of said 'T' would retain the K&N breather. The breather would allow an air draft so as to not create too much vacuum in the crankcase.
The exhaust of the air pump would vent under the car, but I could just as well weld a tube back onto my exhaust system via a one way valve (no cat).
I've read something about a low pressure crankcase helps the oil rings seat better and/or increase horspower by providing less resistance to the piston downstroke at high RPM? Any validity to this?
Thoughts?
Or perhaps I should just run a one way valve to the exhaust, as with race cars. (The exhaust rushing past the crankcase vent inlet creates a vacuum.)
*Exhaust Vent Attempt*
*Working Version*
~thread~start~
As tested, my PCV system was free venting via a K&N breather on the oil filler cap.
My (somewhat unoriginal) new idea is to re-install the air pump, connect the intake port of the air pump to the oil filler cap via a 'T' fitting, the branch of said 'T' would retain the K&N breather. The breather would allow an air draft so as to not create too much vacuum in the crankcase.
The exhaust of the air pump would vent under the car, but I could just as well weld a tube back onto my exhaust system via a one way valve (no cat).
I've read something about a low pressure crankcase helps the oil rings seat better and/or increase horspower by providing less resistance to the piston downstroke at high RPM? Any validity to this?
Thoughts?
Or perhaps I should just run a one way valve to the exhaust, as with race cars. (The exhaust rushing past the crankcase vent inlet creates a vacuum.)
*Exhaust Vent Attempt*
*Working Version*
~thread~start~
Last edited by PorKen; 01-18-2004 at 11:50 PM.
#3
Nordschleife Master

The air pump idea strikes me as fairly clever but I've got reservations. The blow-by is both hot and humid. I'm not sure the pump will last with steam being pumped through it.
I've read about drawing a vacuum in the crankcase. The summary is that "it works" to raise horsepower. Does the air pump have enough strecngth to do that?
Using vacuum of a pitot tube into the exhaust stream is an established practice. There are kits to insert that at header flanges.
The vents from the engine are reasonably large. I don't think the crankcase is pressurizing...and if it is you've got bigger problems.
One last thing: I notice that the breqther is mounted sideways. The element is intended to filter stuff out in both directions. If you're getting a oil misting problem, it'll drip down on the engine. Routing that port to a catch tank is another apporach.
I've read about drawing a vacuum in the crankcase. The summary is that "it works" to raise horsepower. Does the air pump have enough strecngth to do that?
Using vacuum of a pitot tube into the exhaust stream is an established practice. There are kits to insert that at header flanges.
The vents from the engine are reasonably large. I don't think the crankcase is pressurizing...and if it is you've got bigger problems.
One last thing: I notice that the breqther is mounted sideways. The element is intended to filter stuff out in both directions. If you're getting a oil misting problem, it'll drip down on the engine. Routing that port to a catch tank is another apporach.
#4
Inventor
Rennlist Member
Rennlist Member
Thread Starter

Thanks for the replies.
The breather as installed doesn't drip oil at all, in fact, at impulse speeds there are rarely any emissions from there. Occasionally an oily steam vapor wafts out of it.
I drilled out the cap inside to 1/2" when I installed the K&N breather. The hose connection is 1" but at the entrance to the strainer area there is only a ~8mm hole.
I already have the check valve for the air injection system. I could weld a pilot tube (GlenL - thanks for mentioning the tube, I would have just put a surface mount!) into the exhaust after the oxygen sensor(s). Then I would measure the amount of vacuum generated and decide if pumping would be worth the added complexity/HP trade.
On the other hand, I could just stick the pump on there, no welding, and free vent it... No need for the breather (maybe put it on the output side); just let the air pump create as much vacuum as it can.
Regarding the steam: What are the guts of the air pump made of? Stamped steel or aluminum?
The breather as installed doesn't drip oil at all, in fact, at impulse speeds there are rarely any emissions from there. Occasionally an oily steam vapor wafts out of it.
I drilled out the cap inside to 1/2" when I installed the K&N breather. The hose connection is 1" but at the entrance to the strainer area there is only a ~8mm hole.
I already have the check valve for the air injection system. I could weld a pilot tube (GlenL - thanks for mentioning the tube, I would have just put a surface mount!) into the exhaust after the oxygen sensor(s). Then I would measure the amount of vacuum generated and decide if pumping would be worth the added complexity/HP trade.
On the other hand, I could just stick the pump on there, no welding, and free vent it... No need for the breather (maybe put it on the output side); just let the air pump create as much vacuum as it can.
Regarding the steam: What are the guts of the air pump made of? Stamped steel or aluminum?
#5
Nordschleife Master

I think that the body is steel, but what matters is the bearings which will not be aluminum.
If you put in a tube, angle the tip to maximize the suction. I'm thinking that if you did that, you wouldn't need the pump at all.
Do post if you rig up the pump. Mine's just tensioning the fan belt.
If you put in a tube, angle the tip to maximize the suction. I'm thinking that if you did that, you wouldn't need the pump at all.
Do post if you rig up the pump. Mine's just tensioning the fan belt.
#6
Inventor
Rennlist Member
Rennlist Member
Thread Starter

GlenL - I would imagine that the bearings are of the sealed type?
Maybe an electric pump connected via relay to the WOT throttle switch would be better.
On my girlfriends 95 SAAB, the air injection pump is electric, and only operates when the car is dead cold. It runs for <30 seconds until the oxygen sensors warm up.
It is a big beefy pump, unfortunately it costs $300 new!
Try searching for electric vacuum pump on Google; most of the search results were not exactly what I had in mind...
Maybe an electric pump connected via relay to the WOT throttle switch would be better.
On my girlfriends 95 SAAB, the air injection pump is electric, and only operates when the car is dead cold. It runs for <30 seconds until the oxygen sensors warm up.
It is a big beefy pump, unfortunately it costs $300 new!
Try searching for electric vacuum pump on Google; most of the search results were not exactly what I had in mind...

#7
Inventor
Rennlist Member
Rennlist Member
Thread Starter

Upon further research: the answer is no!
The carbon sealing surfaces in the stock pump will fail quickly with oil ingestion and the pump will seize!
However I did find some good reads on 'crank evac':
____Modified belt driven air pump
____Using a GM electric auxiliary brake booster vacuum pump
I just might try the GM electric pump.
"Theoretically everyone who uses a vacuum pump whether it’s electric or belt driven should see an improvement of 2-5 percent increase in HP."
The carbon sealing surfaces in the stock pump will fail quickly with oil ingestion and the pump will seize!
However I did find some good reads on 'crank evac':
____Modified belt driven air pump
____Using a GM electric auxiliary brake booster vacuum pump
I just might try the GM electric pump.
"Theoretically everyone who uses a vacuum pump whether it’s electric or belt driven should see an improvement of 2-5 percent increase in HP."
Trending Topics
#8
Nordschleife Master

Why not tie your crank vent to the a/c by-pass line.
It's not like you'll be getting false air, if any more long. Modify an a/c bypass silinoid so it only opens when the WOT switch is switched on, so your not sucking air into the crank case seals when you let of the throtal.
There's got to be a way to make the TB ventury make your vacuum for you.
You'll amost certainly need to add a major catch can. Maybe serices of baffals and mesh screens to keep any oil mist out of the intake. Oh, I got it, add a can filled with steel wool. Well, filled with steel wool secured by a fine metal screen. Leave the bottem empty, and run a return line back from just below the screen. This away you can drain the water at the bottem off, but the oil that gets collected goes back into the crankcase.
I'll bet that would work well. Maybe solve the GTS oil mist problem...
It's not like you'll be getting false air, if any more long. Modify an a/c bypass silinoid so it only opens when the WOT switch is switched on, so your not sucking air into the crank case seals when you let of the throtal.
There's got to be a way to make the TB ventury make your vacuum for you.
You'll amost certainly need to add a major catch can. Maybe serices of baffals and mesh screens to keep any oil mist out of the intake. Oh, I got it, add a can filled with steel wool. Well, filled with steel wool secured by a fine metal screen. Leave the bottem empty, and run a return line back from just below the screen. This away you can drain the water at the bottem off, but the oil that gets collected goes back into the crankcase.
I'll bet that would work well. Maybe solve the GTS oil mist problem...
#9
Inventor
Rennlist Member
Rennlist Member
Thread Starter

VU - that's basically what the stock PCV does?
Trouble is, you don't (from a performance perspective) want to use engine vacuum because you want high vacuum, and don't want to burn oil vapor (lowers octane), or suck in unburnable water vapor.
I realize now that I should do something though, not having a crank evac system is bad.
More options:
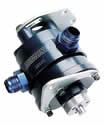
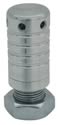
Moroso belt driven pump, $359
Vacuum relief valve, $135 from Summit
Trouble is, you don't (from a performance perspective) want to use engine vacuum because you want high vacuum, and don't want to burn oil vapor (lowers octane), or suck in unburnable water vapor.
I realize now that I should do something though, not having a crank evac system is bad.
More options:
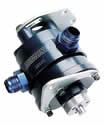
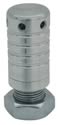
Moroso belt driven pump, $359
Vacuum relief valve, $135 from Summit
#10
Nordschleife Master

Well, use a really good catch can that has enough surface area to condense the oil vapors and no real vapors make it to the engine. From there all that remains is blow by, which is nearly the same as EGR gas, which icreases octane.
I'm not sure how much vacuum the ventury would make, hum...
I'm not sure how much vacuum the ventury would make, hum...
#11
Inventor
Rennlist Member
Rennlist Member
Thread Starter

VU,
The catch can is a good idea. Maybe best put in between the engine and the vacuum source so as not to contaminate the pump. The early cars oil fill is much like a catch can with the screen inside.
Lowering the air pressure in the oil pan gives you more horsepower and torque, but I'm not sure it would be good for the racing GTSs.
Creating a vacuum in the pan lowers the oil pressure because the oil pump has to work harder to pull oil out of the the pan.
Or maybe it would be good:
"With negative crankcase pressure present, the engine's oil pump sees less resistance, therefore the pressure that the gauge will show is lower, but in turn the volume that the oil pump puts out actually increases. Because of the reduced resistance, the oil pump can flow more oil while showing less pressure on the gauge. Since the increased flow serves to pull additional heat away from the bearings and journal, however, the reduced oil pressure is compensated for, and no engine damage occurs"
The catch can is a good idea. Maybe best put in between the engine and the vacuum source so as not to contaminate the pump. The early cars oil fill is much like a catch can with the screen inside.
Lowering the air pressure in the oil pan gives you more horsepower and torque, but I'm not sure it would be good for the racing GTSs.
Creating a vacuum in the pan lowers the oil pressure because the oil pump has to work harder to pull oil out of the the pan.
Or maybe it would be good:
"With negative crankcase pressure present, the engine's oil pump sees less resistance, therefore the pressure that the gauge will show is lower, but in turn the volume that the oil pump puts out actually increases. Because of the reduced resistance, the oil pump can flow more oil while showing less pressure on the gauge. Since the increased flow serves to pull additional heat away from the bearings and journal, however, the reduced oil pressure is compensated for, and no engine damage occurs"
#12
Nordschleife Master

I don't think it would matter.
It take a pressure defferentail to cause the oil to flow into the bearings. The oil pump creates that pressure differential. The oil never sees atmospheric pressure, so we should probably deal in absolute pressure. So if all we're worryed about is the diffrence in pressure between the oil in the lines, and that in the crank case, a vacuum shouldn't cause a problem. The oil pump is positive displacement, so as long as it's good, it's going to deliver the proper flow no matter the crank case pressure.
I would be curious as to the reason that a vacuum in the crank case would create more power however.
On the early cars, the screen is more of a filter so you don't pour paper from the bottel into the engine, than something to catch oil mist. Also, it's apperently not large enough to adquitly catch the mist. You'd need something taller, with a much finer, more extensive mesh, for a larger surface area, to really seperate the mist out.
It take a pressure defferentail to cause the oil to flow into the bearings. The oil pump creates that pressure differential. The oil never sees atmospheric pressure, so we should probably deal in absolute pressure. So if all we're worryed about is the diffrence in pressure between the oil in the lines, and that in the crank case, a vacuum shouldn't cause a problem. The oil pump is positive displacement, so as long as it's good, it's going to deliver the proper flow no matter the crank case pressure.
I would be curious as to the reason that a vacuum in the crank case would create more power however.
On the early cars, the screen is more of a filter so you don't pour paper from the bottel into the engine, than something to catch oil mist. Also, it's apperently not large enough to adquitly catch the mist. You'd need something taller, with a much finer, more extensive mesh, for a larger surface area, to really seperate the mist out.
#13
Banned
Join Date: Feb 2002
Location: Ft. Lauderdale FLORIDA
Posts: 5,248
Likes: 0
Received 4 Likes
on
3 Posts

Porken-
I think your heading into detonation land!
If you have excessive crankcase pressure, then you have have combustion pressure in your crankcase. There's a term for this- "blow by". It means that your rings are bad.
You can recycle the pressure all you want. The problem is that if you run it to the intake, you are forcing motor oil [extremely low octane] into the combustion chamber, most likely causing detonation. My '66 Ford had blown rings- it got 10 mpg, and when I basically ran a tube from the top of the valve cover to the intake via the existing PCV valve it started running bad. I decided to let the oil that blew by go from the tube into a metal juice can with a fitting soldered on. Then all I had to do was empty the can every couple hundred miles....
N!
I think your heading into detonation land!
If you have excessive crankcase pressure, then you have have combustion pressure in your crankcase. There's a term for this- "blow by". It means that your rings are bad.
You can recycle the pressure all you want. The problem is that if you run it to the intake, you are forcing motor oil [extremely low octane] into the combustion chamber, most likely causing detonation. My '66 Ford had blown rings- it got 10 mpg, and when I basically ran a tube from the top of the valve cover to the intake via the existing PCV valve it started running bad. I decided to let the oil that blew by go from the tube into a metal juice can with a fitting soldered on. Then all I had to do was empty the can every couple hundred miles....
N!
Last edited by Normy; 11-16-2003 at 11:49 AM.
#14

Originally posted by PorKen
I've read something about a low pressure crankcase helps the oil rings seat better and/or increase horspower by providing less resistance to the piston downstroke at high RPM? Any validity to this?
I've read something about a low pressure crankcase helps the oil rings seat better and/or increase horspower by providing less resistance to the piston downstroke at high RPM? Any validity to this?
Originally posted by GlenL
I've read about drawing a vacuum in the crankcase. The summary is that "it works" to raise horsepower. Does the air pump have enough strength to do that?
I've read about drawing a vacuum in the crankcase. The summary is that "it works" to raise horsepower. Does the air pump have enough strength to do that?
The vents from the engine are reasonably large. I don't think the crankcase is pressurizing...and if it is you've got bigger problems.
Originally posted by GlenL
If you put in a tube, angle the tip to maximize the suction. I'm thinking that if you did that, you wouldn't need the pump at all.
If you put in a tube, angle the tip to maximize the suction. I'm thinking that if you did that, you wouldn't need the pump at all.
Originally posted by ViribusUnits
You'll amost certainly need to add a major catch can.
You'll amost certainly need to add a major catch can.
Originally posted by ViribusUnits
I'm not sure how much vacuum the ventury would make, hum...
I'm not sure how much vacuum the ventury would make, hum...
Originally posted by ViribusUnits
I would be curious as to the reason that a vacuum in the crank case would create more power however.
I would be curious as to the reason that a vacuum in the crank case would create more power however.
#15
Inventor
Rennlist Member
Rennlist Member
Thread Starter

Normy - I don't notice much blowby; the whole point is not to put any blowby/oil mist/water vapor back into the engine anyway.
Zed - thanks for the input.
Went to the 'yard today, but couldn't find one of these:
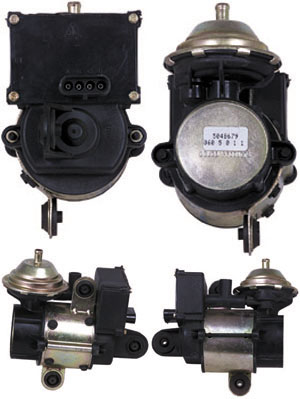
Cardone 641500 - remanufactured brake booster vacuum pump
I checked online at NAPA and PartsAmerica (search for 641500) ~$160 with a $20 core.
I then called locally (82 Cadillac Cimmaron) and may have found one for $150 with no core.
I'm thinking about mounting this suction side down in the drivers side fender where the cruise motor was, with a catch can underneath/before it.
Supposedly it kicks in automatically at 5" vacuum and can pump down to 16" at 13.7V.
I plan to route the regular PCV intake vacuum from the throttle body (through a one way valve connected to the pump vacuum circuit) for low speed operation. Then at WOT the pump should come on when manifold pressure drops. While the pump is running, the one way valve from the TB will be pulled shut until the pump shuts itself off.
Zed - thanks for the input.
Went to the 'yard today, but couldn't find one of these:
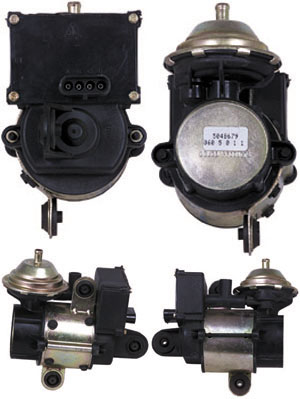
Cardone 641500 - remanufactured brake booster vacuum pump
I checked online at NAPA and PartsAmerica (search for 641500) ~$160 with a $20 core.
I then called locally (82 Cadillac Cimmaron) and may have found one for $150 with no core.
I'm thinking about mounting this suction side down in the drivers side fender where the cruise motor was, with a catch can underneath/before it.
Supposedly it kicks in automatically at 5" vacuum and can pump down to 16" at 13.7V.
I plan to route the regular PCV intake vacuum from the throttle body (through a one way valve connected to the pump vacuum circuit) for low speed operation. Then at WOT the pump should come on when manifold pressure drops. While the pump is running, the one way valve from the TB will be pulled shut until the pump shuts itself off.
Last edited by PorKen; 11-23-2003 at 12:34 AM.